New Chapter in Reliability Efforts
Published
by Bob Hance on Tuesday, February 4, 2020
in
Community
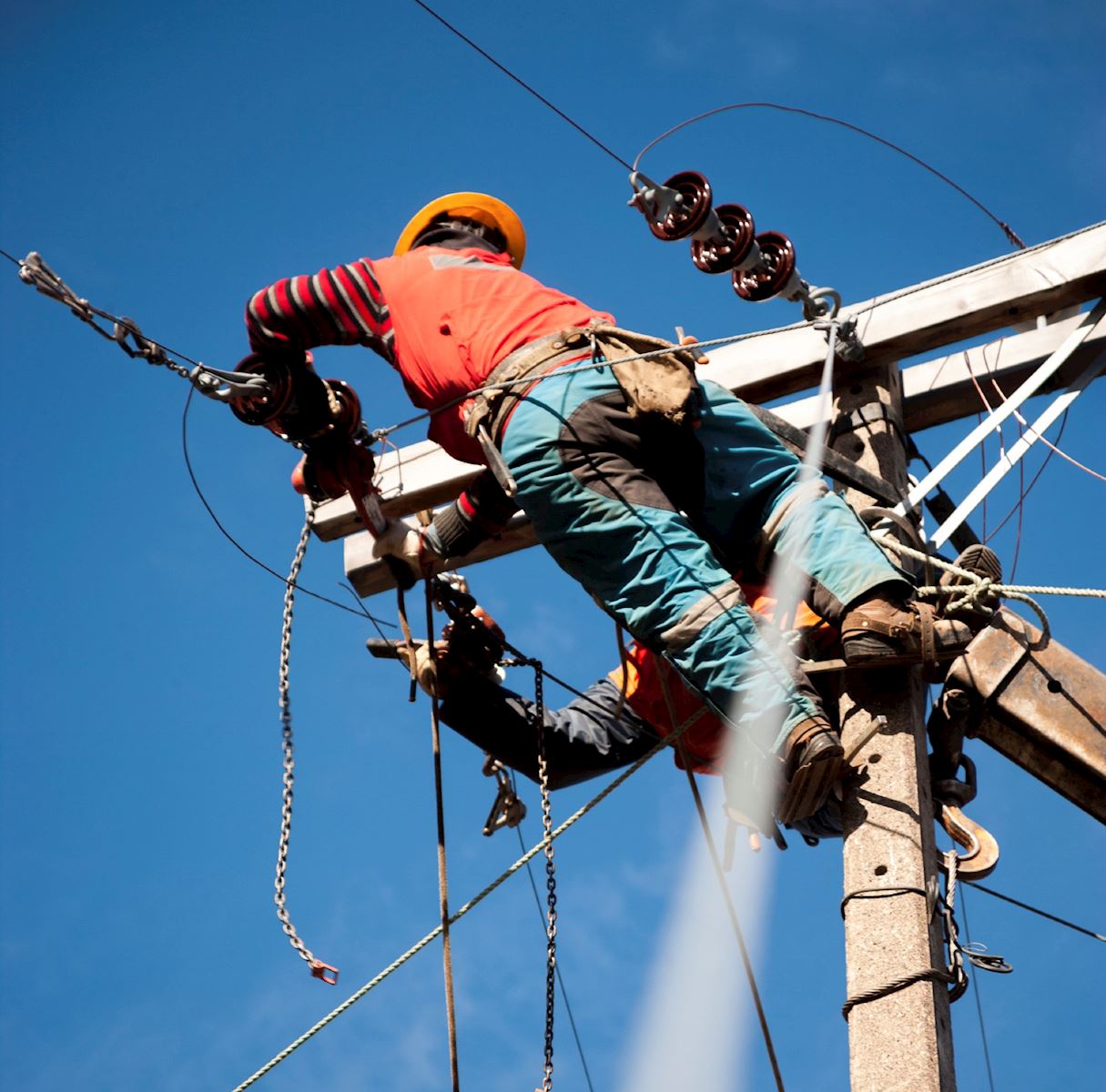
Our work can often be likened to a complicated mystery. When electric outages are tied to a weather event or an accident, it’s typically pretty easy to get the heart of the issue and restore service. However, sometimes our lineworkers must look deep and unearth one or a series of clues to find the source of reliability issues.
We recently had recurring blinks on a line in the northernmost portion of our southwest Michigan service territory. Our highly-trained, super sleuth linemen followed the regular protocol and steps to figure out the issue when they discovered something surprising and, quite frankly, astonishing. They removed a 1940s era lightning arrester, one of many devices on our system that is critical to the delivery of safe and reliable electricity. It was likely an original piece of equipment that, much like the iconic Energizer Bunny, just kept going and going and going. Needless to say the equipment was replaced and issues resolved.
I’ve said many times that an electric distribution system is nothing short of an engineering and mechanical marvel. There are so many pieces and parts that must work together in order to get the electricity from the substation to your home or business, and failure from one of those pieces or parts can cause reliability issues. Many different pieces of equipment, including over 1700 protective devices and nearly 27,000 transformers, are located on or around our 4,200 miles of overhead and underground lines and 72,000-plus poles in order for us to make electricity available to our 36,157 accounts.
We’ve spent tens-of-millions of dollars over the last decade on proactive reliability measures, specifically related to line clearance efforts. It’s made a huge difference in our customers’ service experiences, but we now realize it’s not enough.
In order to keep our engineering and mechanical marvel working, we’re implementing a new level of proactive maintenance, specifically related to identifying aging equipment and infrastructure and updating it before it becomes a problem. Like our line clearance efforts, this is a long-overdue step and will take many years for full implementation, but will ultimately result in an improved service experience.
Operations and maintenance is the second largest bucket of our expense budget, eclipsed only by the cost of purchased power which accounts for almost 60% of our total expenses. In 2020 and beyond, we are escalating our commitment to investing in our system in a strategic and proactive way to improve system functionality and reliability. In November your board of directors approved a $63 million Rural Utilities Service (RUS) loan application. Among other things, these dollars will be applied to our construction and maintenance work plans as an investment in your service experience.
We can’t prevent all outages; it’s simply impossible with a largely outdoor and complex mechanical infrastructure. However, we can take proactive steps to reduce the number and duration of outages, and look forward to sharing the results of those steps as reliability improves.